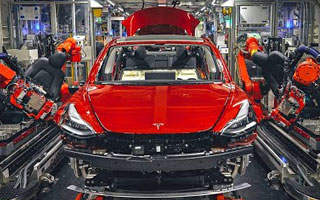
Top 5 Use Cases of Computer Vision in Manufacturing in 2022
Computer vision has been around for decades, but in recent years, this technology has been advancing by leaps and bounds. Computer vision is an application of artificial intelligence (AI) that's able to understand and interpret images, identifying and reacting with near-perfect precision due to developments in neural network technology. In fact, the accuracy of the technology has gone from 50% to 99% in less than a decade.
This article explores 5 computer vision use cases in the manufacturing sector that can help business leaders make better decisions and plans for their computer vision investments.
1. Automated assembly
Consumer expectations for high-quality products are rising, and maintaining high-quality requires precision and consistency. To achieve this quality, many businesses are automating their production lines to eliminate human error by transferring repetitive tasks to bots.
Computer vision systems combine the human eye and the processing power of the computer to automate product assembly for higher efficiency, consistency, and productivity.
Tesla is a good example of a highly automated manufacturing facility:
However, some claim that since humans have adaptive intelligence, they can not be fully replaced by automation. Therefore a collaborative or synergetic approach to automation is considered more successful. Tesla also realized this as they faced various issues and re-designed their manufacturing to make it collaborative with humans and automated machines working together.
2. Predictive maintenance
Heavy machinery and equipment operating in manufacturing facilities degrade over time; this can lead to faults and down-times. These down-times can be expensive and can lead to substantial losses. Computer vision technology can enable consistent and accurate monitoring of production machinery and alert engineers for maintenance before the issue occurs.
Combined with IoT and deep learning, these computer vision-driven predictive maintenance systems can deliver high accuracy and consistency.
Organizations in the oil and gas sector such as Royal Dutch Shell, ExxonMobil, and Chevron leverage predictive maintenance to monitor their machinery for faults and malfunctions.
3. Product quality inspection
Every manufacturer wants products leaving the assembly line to be defect-free; however, this is a challenge because products can often have defects. Checking products on the conveyor belt for defects can be a highly repetitive and error-prone task if done manually.
This task is automated by implementing a machine vision product quality and defects inspection system deployed through high-definition cameras, which inspect all products on the conveyor belt with image and video annotation.
These systems are highly accurate and much more efficient than manual quality inspection.
4. 3D vision monitoring
3D vision monitoring refers to the inspection of the production process’ 3D model created by a computer vision system. This system creates an accurate model of the production process and monitors this process through multiple cameras to identify faults or errors.
For instance, in an automotive vehicle assembly line, if a component is not fitted properly, the system can notify the engineer to avoid malfunctions.
Watch how this 3D vision inspection and sorting production line operates.
5. Improved safety
Working in a manufacturing facility can be risky since it involves working around and with heavy machinery and sometimes in extreme temperatures. Usually, factories have surveillance systems mounted by an employee to monitor the workers. This manual inspection can be tedious and inefficient.
A computer vision-enabled safety monitoring system in a manufacturing facility can monitor workers from the entrance to exit to ensure all safety regulations and rules are followed. If an incident occurs, the system deployed by high-definition cameras will alert medics or relevant authorities.
Watch how Dow, an American multinational chemicals company, leverages computer vision and AI to improve worker safety.